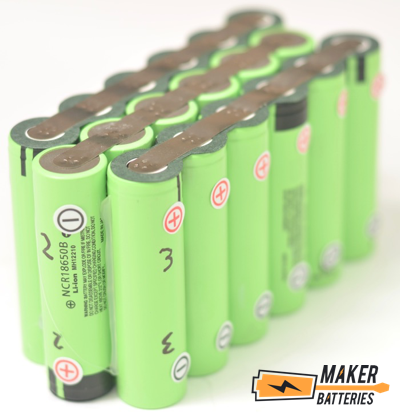

The 1s6p modules from Maker Batteries are great for building large capacity batteries. At just over 20AH each, a single series chain of modules can create a large 20AH battery pack. In this tutorial I’m going to assemble a small 12V 20AH pack, but you can build a larger 24V, 36V or 48V pack with these same instructions by simply adding more cells in series.
Step 1: Measuring each module’s voltage
To start, I’m going to lay out all of my modules and measure their voltages. They should all be within a couple hundredths of a volt. They were checked at the factory and again before shipping, but this is just a sanity check right before we build the battery to triple check that all of our cell modules are good.
Step 2: Laying out the cell modules
For these 6p straight modules, the number of different possible layouts is fairly limited. You don’t have as much creativity as with the triangular modules. The two major layouts are either straight packing or offset packing, demonstrated in the two pictures below.
Straight packing will give you a narrower but longer battery, while offset packing will make a wider battery with less total volume. This is because offset packing is more efficient by leaving less space between the cells. It also gives you twice as much surface area to apply the hot glue (each cell touches the next row in two places instead of one).
The difference between straight and offset packing doesn’t seem like much on such a small battery like this 12V pack, but when you get up to larger batteries like the 13 module 48V20AH battery kit below, offset packing can make a big difference in the length of your final battery.

Regardless of the type of packing you go with, remember that you’ll need to place every other module upside down in the pack so that you can easily solder the cell modules in series. Your pack should look like this, depending on the voltage:
Now you can go ahead and glue your cell modules together. Use hot glue liberally and make sure you’ve got a nice strong connection between cells. These packs start to get heavy as you add more modules, so make sure you’ve got a good glue joint to keep them together. If the glue joint happens to fail while you’re working on the pack, just shoot some more glue in the spaces between cells. Be careful not to short the pack later on with the metal tip of the hot glue gun though!
Step 3: Labeling the cell modules
Next, label your cell modules so that while you’re working you can easily see which end of the cells is positive and negative, as well as which cell module is which. I like to add the positive and negative stickers included in the Maker Batteries kit to the cells, and then write the cell module numbers onto the cells themselves. You can skip the stickers if you just want to write “+1”, “-1”, “+2”, etc onto each cell.
Remember that the end of the cell with the green paper insulation is the positive end (anode). That’s also the cell with the black bands on the heat shrink wrapping. These green Panasonic 18650B cells also conveniently have the + and – signs printed on the sides, though they are pretty small and don’t stand out, which is why I like to add the stickers.
Step 3: Tinning the cell modules
Now we are almost ready to begin soldering our modules together. To prepare for this though we’ll need to tin our cell modules. Tinning is the practice of heating something and applying solder to it. This pre-soldered, or tinned, surface will more easily accept whatever we will be soldering to it next (which in our case is another nickel strip).
On our cell modules we want to make a connection between each individual cell, so that’s where we are going to tin our modules: on the nickel strip between the cells. Start by turning your pack over to the side where you can see the +1 module and the -2 module terminals right next to each other, like in the photo below.
The process I used to tin the nickel strip on the modules above is this: apply heat from a good, adjustable temperature soldering iron to the point between the cells for about a second, followed by solder applied directly to the point between the soldering iron and the nickel strip. It’s ok to touch the solder to the soldering iron. Leave the tip of the soldering iron there for about one more second until you see the solder blob spread out and blend into the nickel strip. Now remove the soldering iron.
Using good quality 60/40 lead solder will help make this process easier. The lead solder isn’t very healthy to breathe but it solders beautifully. Just make sure to work in a well ventilated area. Open a window and use a fan to blow the air away from your face and workstation. Just make sure the air isn’t blowing your nickel strips around which could potentially cause a dangerous short if they land in the wrong place.
Here’s an illustration of how the tinning process should look. Notice that the soldering iron spends no more than a couple seconds in contact with the cell module. Though this is a different cell module, the idea is the same.

Step 5: Cutting your nickel strips
Your nickel strip roll will need to be cut into short sections of about 3/4″ or 2 cm long. Cut a few at first to double check that the size is correct. I generally just eyeball it and don’t use a ruler; the exact length isn’t critical. Just make sure they aren’t so short that you can’t easily solder them and aren’t so long that they extend past the nickel strip on both modules.
Use an ordinary pair of scissors to cut the nickel strips into shorter pieces. If you find that you are getting a bit of a bend at the end of the nickel strip, just push the corner flat onto your table to bend it back so it is straight.
If you are using offset packing, you might find it easier to cut your nickel strips into parallelograms instead of straight rectangles. This way your edges will line up with the nickel strip already welded to the battery cells. See the illustrated diagram below in Step 6.
Step 6: Soldering the nickel strips
The process of soldering the nickel strips should be done fairly quickly in order to avoid heating up the battery cells. The whole process should last about 2-3 seconds at most, though you can get probably get it down to under 2 seconds once you get the hang of it.
This is where the chopstick, tooth pick, popsicle stick or other piece of wood is going to come in really handle. The basic process I use for soldering these nickel strips is this:
- hold chopstick in my mouth (for easy reach when transferring to my hand)
- place nickel onto module so it overlaps the solder blobs I already tinned
- hold soldering iron in one hand and solder in the other
- place tip of soldering iron on edge of nickel strip to heat it while touching solder to iron and nickel strip
- merge the pre-tinned solder blob on the module into the new solder blob I just applied to nickel strip
- simultaneously during solder merging, drop solder and pick up chopstick
- use chopstick to hold down nickel strip then remove soldering iron – wait 5 seconds until cool.
It sounds complicated but it’s a really smooth 2-3 seconds once you get the hang of it. Basically, hold the nickel strip with the soldering iron while adding fresh solder then hold the nickel strip down with a chopstick until it cools. The end result looks like this:
You’ll need to make all of your series connections between +1 to -2, and then flip the battery over to work on the other side. That’s where we’ll make the next connection between +2 to -3. For our battery, that will be the last series connection, since we only have 3 modules. If you were making a 24V battery though, you’d have 6 series connections total (connecting 7 modules). I like to do all of the connections on one side of the battery first, and then turn the battery over and complete the series connections on the other side of the battery. When you’re working with big 36V and 48V batteries, it means you do a lot less flipping of the battery that way.
When you are performing these series connections you must be extremely careful that you do not short circuit your battery. This can happen by accident if you dropped a piece of nickel strip in the wrong place, or if it simply moved a bit while you were soldering it. For example, if you’ve already completed the series connections between +1 and -2, then flip the battery over to work on the connections between +2 and -3, any conductor that bridged the terminals between -1 and +2 would cause a large spark as it short circuited your battery. If that happened for just a split second, things would probably be fine, though your battery cells wouldn’t be happy about it. If something heavy gauge fell on those connections though and the connection remained constant, your cells would quickly overheat and could begin venting smoke and other gases. You want to avoid this situation so be very careful while working to not let anything short circuit the terminals of your modules.
After you’ve finished soldering all of your series connections, perform a sanity check by measuring the voltage from your -1 terminal to your highest + terminal, in this case the +3 terminal on this 12V battery. You should see your total pack voltage, which on this 12V battery is about 10.575V on these partially discharged cell modules. If you aren’t getting a voltage that is the sum of your cell modules, you must have missed a connection somewhere. Go back and double check that you’ve soldered all of your connections correctly.
Step 7: Adding on your BMS
Now we are ready to add the Battery Management System (BMS) to our battery. I generally like to place the BMS on the end of the pack so that it doesn’t add a lump on the side of the pack.
You can either hot glue it directly to the edge of the pack, or you can take the smaller strip of foam that came with your kit and cut a patch to sit between the BMS and the pack. The foam will add a little more shock protection if you’re using the battery in a situation that will see a lot of movement or vibration such as on an electric bike. If the battery will be stationary most of the time though, simply gluing the BMS down is perfectly fine.
You’ll notice in the photo above that I’ve gone ahead and tinned the strip of nickel on the +3 terminal of the pack. That is because next we’ll need to attach the positive end of the discharge cable. You can either leave your discharge cable the length it is, or you can cut it back to make it shorter. If you’re making it shorter, trim the thick red discharge cable coming from the yellow XT-90 connector to whatever length you’d like. Make sure to lay it out the way you plan to have it exit the battery to ensure you have enough cable slack to make it all the way out. In this example I’m just going to leave it the same length.
Strip the cable back far enough to expose a length of wire that can be soldered all the way along the positive terminal of the battery spanning the 6 cells in the last module. A helping hands device comes in very handy at this stage to help hold the wire. Be extremely careful not to let the wire touch anything but the +3 terminal or you could create a short circuit. Because the individual strands in that wire can now become unwieldy, I like to solder along the length of that exposed wire, tinning it and keeping it from unraveling. A helpful tip is to do this in stages as you slide off the silicone insulation. Instead of pulling it off all at once, pull it off about half way, tin the exposed wire, then continue pulling the insulation progressively further while tinning the wire each time. You’ll get to the end and have a nicely tinned wire by the time you pull the insulation all the way off.
Now you can go ahead and solder the red discharge wire onto the +3 terminal (or whichever is your highest # terminal on a larger battery). Again, helping hands come in really useful here. The best method is to tin the wire at increments that match the tinned spots on the wire. Next, while the helping hands hold the wire in place, solder the very tip of the wire to the last spot on the +3 module, in between the last two cells. Next, solder a spot closer back towards the base of the wire. Soldering closer to the base of the wire now will keep you from accidentally heating up the first solder joint enough to cause it to flow and release. Now go along and solder each of the individual locations along the length of the wire to the nickel strip as shown below.
Once you have the positive discharge wire soldered onto the last module, go ahead and solder the thin red positive charge wire onto the same location. You can even solder it right on top of the thick red positive discharge wire.
Now you’ll need to solder on the BMS’s thick black wire to the -1 terminal. No matter what voltage battery you are building, this thick black wire goes on the -1 terminal. You’ll likely need to trim it back to whatever length is necessary for your battery. The process of soldering it on is exactly the same as the thick red wire you just did previously, except that it will go on the -1 terminal.
Next you’ll need to solder on the thin balance wires from the BMS. On the BMS I’m using here, all four wires are white. Generally the first wire will be black, and that will be the -1 wire. You can solder that one on first straight to the -1 terminal. If it’s easier you can solder it directly on top of the thick black wire you just soldered previously. Continuing, the next wire in the line of thin balance wires will be the +1 wire, which goes on the +1 terminal of module 1. The next wire is +2, and the last wire in our case is +3. Since we have a 3s battery, we only have 4 wires. A 10s battery will have 11 balance wires and a 13s battery will have 14 balance wires. There’s always one more wire because the first module gets a wire soldered to both the -1 and +1 terminals.
The last wires you’ll have to deal with are a set of two wires exiting the BMS. These are for adding a switch. If you wanted to add an on/off switch to your BMS you could add it here by connecting the two wires with a toggle switch. Connecting the two wires and completing that circuit turns on the BMS, while disconnecting the two wires and breaking that circuit turns the BMS off. This could be helpful if you plan on leaving the battery dormant for a long time without using it as it’s a handy way to ensure the battery is off. Otherwise, it’s not really a necessary feature. I’m just going to solder these two together and add a piece of heat shrink. This way my BMS is always ‘on’ and ready to go.
Depending on the model of BMS in your kit, your two wires might come as a loop. If that’s the case, just leave them the way they are if you don’t need a switch, and if you do want a switch then simply cut the wire and solder the two sides onto a toggle switch.
Now that we’ve taken care of all the wires, it’s time to tape everything down. I like to use kapton tape, a non static, heat resistant tape. You can use electrical tape too but I don’t like how it gets gummy and isn’t as strong as kapton tape.
Just tape down all your wires so that they are flush with your battery and won’t vibrate or chafe on any of the nickel strips.
This is another good time for a sanity test to ensure everything is correctly connected. Measure the voltage at your charge and discharge connectors to ensure you’re getting the correct pack voltage for your partially charged pack. You can insert your digital multimeter probes directly into your yellow XT90 discharge connector to measure the voltage there. For your charger connector, it’s better to take the extra connector that came in your kit and plug it into the charge port. But first make sure the two bare wires on the end are spread out and not touching, otherwise they can short and fry your BMS. Now you can measure the voltage of your charge connector as well. As long as both are giving you the correct pack voltage then you’re golden. If not, double check all of your connections to find where something isn’t correctly connected.
Step 8: Sealing your battery
Your kit comes with both foam and heat shrink tubing for sealing up your battery. If your battery will be sitting in one place its whole life then you might not need the foam. It’s there for applications like electric bicycles and other uses where the battery will see a lot of motion, vibration and generally live an active life. If you don’t need the foam, skip to the heat shrink section. For the rest of you, start with the foam.
Lay your battery out on the foam sheet with the paper backing still on. Wrap the foam around your battery to ensure that it’s the right size. If it’s too big, trim some off with a pair of scissors.
Once you’ve got your foam down to the proper size, remove the yellow backing and wrap the foam around the battery. To cover the ends of the battery, cut a couple pieces of foam off of the second strip of foam supplied in the kit. Remove the paper backing and stick those pieces onto the ends of the battery.
Now that your battery is all nice and cozy in its foam shell, you’re ready to add the heat shrink. Start with the piece that is wider and slide it around the widest part of the battery. You want about 3/4″ or 2 cm extending on either side of the battery. This overlap will shrink down and hold the sides of the battery, keeping the shrink wrap firmly in place. If there is too much overlap then it won’t shrink down all the way and you’ll be left with wavy edges that can be annoying to cover. Be careful not to cut off too much though. Err on the side of caution and leave it a bit long if you’re unsure. You can always go back and trim the edges back after you’ve shrunken the heat shrink, it’s just a tad bit trickier.
At this point you can use either a heat gun on a low setting or a strong hair dryer on its highest setting. Just don’t turn your heat gun up too high because you can actually melt heat shrink with a strong heat gun. Apply even heat around the heat shrink until it’s completely shrunken around your battery.
Next, slide your second, thinner piece of heat shrink along the battery. This time, make sure you’ve got only about a 1/2″ or 1.5 cm of overlap on each side, since the heat shrink has less room to shrink this time. On this piece of heat shrink, I like to start by shrinking the ends first to ensure they get a good wrap on the edges of the battery, then move towards the middle. Try to spread the heat around though and shrink all the sections equally instead of one section and then another.
Lastly, apply your logo so that everyone knows that this is a Maker Battery that you built yourself!
And that’s it, congratulations! You’ve just built your very own lithium battery! What are you going to use it for? Have a cool project you’re working on? If you document your project and want to share it with us, we might feature it on the community projects page to inspire others. Drop us a line and let us know what you built!